认 证:工商信息已核实
访问量:1197878
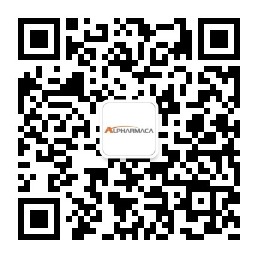
上海奥法美嘉生物科技有限公司 2021-03-10 点击606次
Application Note AN–CMP10
Analyzing Large Particles in CMP Slurries 分析CMP Slurry中的大颗粒
化学机械抛光(CMP)工艺的质量取决于抛光设备和浆料,浆料由包含多种化学添加剂的液体中定义明确的固体颗粒组成。当今主要的生产问题之一是根据浆液的规格保证其质量,以及在使用时(POU)免受任何形式的降解的稳定性。许多浆料是不稳定的胶体体系,具有相对较短的保存期限。同样,将浆液从容器传输到CMP工具可能是由于剪切,沉降或团聚而导致降解的原因。影响浆料性能的一个关键方面是在CMP过程中会导致缺陷(例如晶片上的微划痕)的大颗粒的存在。
在这里,我们对微电子制造工厂中使用的商用CMP浆料进行详细分析。由于这种特殊的浆料会引起微划痕,因此我们使用扫描电子显微镜检查了其粒径分布,以区分出形成大颗粒的可能原因。与CMP过程工程师密切合作进行的这项研究用于故障排除。
CMP工艺有缺陷
该研究是在有缺陷的CMP工艺运行后开始的;从不同批次的相同类型浆料中选择样品进行比较。对于每个样品,表1列出了浆液批号,取样位置(移动罐或分配系统),CMP后在晶圆上观察到的平均微划痕数以及微滤器的影响(1.5μm)在POU之前。另外,我们已经报道了使用来自粒度测量系统公司(PSS,加利福尼亚州圣巴巴拉)的光散射Accusizer 780仪器测量的大颗粒(> 2.1μm)的总密度。
除参考样品外,该列表对应于在工厂中进行的CMP运行的实际顺序。由微划痕揭示的缺陷的第一个迹象出现在299号批中(PLY缺陷的正常水平为96.5%)。将浆料容器更改为批次322无法解决问题,并且微划痕的数量继续急剧增加。批号322与新批号310混合在一起,并且在POU上安装了微过滤器,但这并不能立即解决问题。最终,由于再次使用批次322时,微划痕消失了,微过滤器开始起作用。有限的一系列实验的过程结果似乎令人惊讶,特别是当考虑到降低过滤孔隙率并不能立即解决问题时。这意味着可以先验地考虑以下几种原因:
· 浆料的制造不良,不符合参考样品的原始规格。
· 移动罐中的泥浆被污染或降解。
· 浆料分配系统中的降解(剪切或沉降的影响)。
· CMP工具本身受到污染。
但是,仅测量大颗粒(> 2.1μm)的总体浓度显然不足以完全决定这些替代方法。 请注意,参考样品已经包含〜7400颗粒/ mL,在40-200 nm的指定正常范围之外。
扫描电镜观察
在以液体形式取样之后,将浆液进行短时干燥预处理并在过滤器支架上进行制备,这不会导致任何其他颗粒污染。 然后将制备的样品引入SEM设备中,以观察和近似计数不同类型和尺寸的颗粒。
Figure 1: Small slurry particles in the specified size distribution.
图1显示了所有在指定范围内的原始浆料颗粒集合。 然而,这些小颗粒中的一些趋于形成微米级的附聚物。 这些可以分为两类:弱结合的团块,显然仅通过范德华相互作用来连接(图2a)。 牢固粘结的合金显示出部分烧结的迹象(图2b)。 此外,这些牢固结合的团聚体中的一些团聚体可以达到非常大的尺寸(最大10μm),并呈现出具有相对尖锐角度的不规则形状,如图2c所示。
a) weakly bonded agglomerates b) strongly bonded agglomerate c) large agglomerate with sharp angles
Figure 2: Agglomerates of small slurry particles:
除参考样品外,在所有样品中也观察到完全不同类型的颗粒。 它们由完美球形的球形颗粒组成,它们大多数在微米大小的范围内,并且通常被小的浆料颗粒覆盖(图3a)。 但是其中一些球形颗粒达到了10μm(图3b)。
Figure 3: Ball-like particles present in slurries from lots #299 and #322 and due to a defective slurry manufacturing process.
讨论
表2概括了表1中显示的一系列样品中不同类型的团聚体和球形颗粒的出现。值得注意的是,在参考样品中只能检测到弱结合的团聚体,因此可以解释大于2.1μm的7400颗粒/ mL,用Accusizer 780测量。但是,在生产中使用的所有浆料批次中,甚至在直接从移动储罐中取样的样本中,都观察到了无论大小,都非常牢固的团聚体。
这表明它们未在分配系统中形成,但可能是由于浆料在其容器中的沉降和老化所致。 但是,在浆液的储存或分布的温和温度条件下,批号322中观察到的大球形颗粒无法通过任何小颗粒的烧结过程形成。 因此,它们肯定是在这些特定批次的有缺陷的浆料制造过程中生产的。
通过比较这些结果和表1中的观察结果,可以得出微划痕主要是由最大的团聚体和最大的球形颗粒(批号322)引起的,而亚微米的团聚体和球形颗粒则具有不可检测的影响, 至少对于此特定的CMP过程。
结论
至关重要的是要确保注入CMP工具中的浆料的粒度分布,以避免严重的缺陷,例如微划痕。 在这方面,浆料制造商给出的原始粒度规格不足以保证。 有几种因素会导致浆料降解,包括沉降,老化和容器中的部分烧结,这会形成牢固结合的团块。
浆料制造过程中的事故也是可能的,从而导致大的球形颗粒。 在POU处进行微过滤,并使用常规的粒径监测仪对> 2.1μm的颗粒进行整体测量可以解决该问题,但是更精细的分析对于追踪大颗粒的起源很有用。 尽管在这项研究中分析的样品数量有限,但SEM仍可以根据颗粒的类型和形状对其进行区分,并且揭示了加工晶圆上微划痕的真正起因。